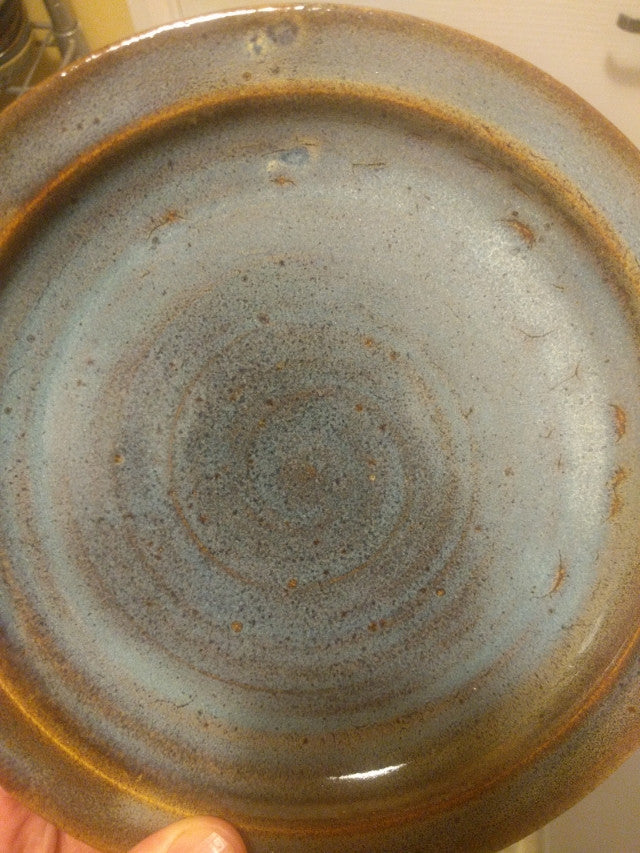
Avoiding Pesky Pin Holes and Glaze Dimples with Proper Carbon Burnout
Share
I had a very unhappy kiln opening a few weeks ago with glaze dimples and pin holes all over my bigger pieces. I’ve had the problem on a smaller scale before, but nothing to this extent. It’s quite soul destroying finding a load of work that needs to be binned. I sulked for a couple of days, then with gritty determination I vowed to find a solution!
Glaze pin holes and dimples – how to solve it?
Initially, as a glaze defect I began pointing fingers at the glaze. The pieces in question have been glazed in two different layered glazes. This is a new technique for me and it was quite possibly the culprit. The only problem was many of the smaller items in the same load had the same glaze and had come out fine.
Next I tried to blame the clay. I use a heavily speckled stoneware which is said to be more troublesome than purer clay mixes. But again, the smaller pieces made from the same clay had turned out fine.
Can the bisc fire cause glaze pinholing?
The factors linking the most problematic pinholed pieces was their size, and the fact I stacked them during the bisc. It was my nine inch pasta bowls and plates. I had used sand to prevent stress on the rims but they were very densely packed. The more I read, the more it seemed the bisc firing was the problem.
I fire my kiln manually – I’m too poor for any fancy electronic controllers. I have got used to a slow heat up until all moisture is gone, then pretty much push it to the max until the kiln sitter drops.
It seems the lack of carbon burnout was causing the problems with glaze pinholing in my case. I would say there were a number of contributing factors in my case.
- Kiln schedule too short. Mainly in the red heat range around 700°C to 800°C
- Pots stacked too tightly together
- No kiln ventilation
- Impure clay?
- Larger pieces taking longer for heat to penetrate to the core and properly burnout carbon
Total carbon burnout – reduce pinholes with a three pronged attack.
I tried another bisc firing and changed a number of things.
- I changed the firing schedule. I now think the pots may need longer at temperatures where carbon burnout takes place. Each carbonate burns out at a different temp so there is no exact figure. In my case I kept the kiln at a red, slightly orange colour which is around 700°C to 800°C. Overall bisque firing was around 4 hours longer than usual.
- I decided to build a DIY kiln vent which I have writen about in a separate post. It’s hard to say how much of an impact the vent had, as I changed other variables too. Hopefully I can get a better idea in future testing.
- I separated pieces better in the kiln. I used little clay pyramid props between plates instead of sand. This gave more room to oxygen to enable the burnoff process. I also stacked the kiln with less pots overall. ( The stacking of pots on pyramids turned out to be a really bad idea. They warped during firing at the points they were supported at.)
Results – carbon burnout not the problem?
I wrote most of this article while the kiln was firing. I hoped to add a successful conclusion at the end and live happily ever after!
Unfortunately even after all my best efforts on the carbon burnout front, the resulting plates were almost exactly the same as the previous batch.
I’m pretty sure the kiln vent is working as intended due to my flame tests. Even if it isn’t, the few pots I bisc fired must have had plenty of oxygen round them.
Possible other causes of pinholes to explore
I have taken a closer look at all the pots using this particular glaze. On the whole the bigger items have more pinholes. On the smaller olive dishes it seems the ones with more glaze have no pinholes but a slightly orange peel type surface. This would suggest the glaze may be a bit under fired.
I hadn’t meant to apply less glaze to the bigger items. During dipping I’ve keep the time in glaze the same as for smaller items. I should really dip the larger ones a bit longer as they take more time for a good layer to adhere.
I’ve decided to try modify the glaze with additions of extra frit in varying amounts to each layer. Hopefully a lower melting glaze might seal up the pinholes and smooth out the orange peel surface a little.
If I have no luck with that I have also bought a different clay to try. It’s an off-white stoneware with no speckles. It will probably effect the appearance of the glaze but the colours could be adjusted if necessary.
Changing firing cycle to stop pinholes
Edit: I wrote the rest of this article a while ago. Since completing it I continued to have problems with pinholes, although switching to a white clay without speckles did help somewhat. I'm now firing in a gas kiln.
I didn't want to change my clay just because of glaze defects - I like the look of speckled clay. No matter what I've tried to adjust my glazes I have always struggled with pinholes. They problem is often worst on larger pieces such as plates and vases.
Finally, after my last firing I seem to have a solution - although time will tell if this was just a flute.
I read an article about using a longer firing cycle to avoid pinholes. For my last firing I held @ 1120C for 30 minutes, then climbed slowly until cone 8 was down. Then I dropped the temperature to around 1230C and held for 20 minutes before turning off the gas and closing the kiln up.
Previously I have just fired straight up until the cones drop, then turn off the kiln. I think as I have a very small kiln, the glazes are not able to develop properly with this fast firing style.
I also fired the bisque load to a slightly cooler temperature, perhaps this had some impact on the results.
Out of the thirty or so pots from my last firing none had any noticeable pinholing. This was using glazes that have had problems with it before. Fingers crossed I continue to have success in the future.